What is Safety Data Sheet (SDS)?
A Safety Data Sheet (SDS) (previously, Material Safety Data Sheet) is a document that provides detailed information about the potential hazards, safety precautions, handling procedures, and emergency response measures for a particular substance or product. It includes information about the physical and chemical properties, toxicity, health effects, storage requirements, and disposal methods. The SDS is typically prepared by the manufacturer, importer, or supplier of the substance or product and is an important resource for ensuring safe handling and use of hazardous materials.

Why you need to comply with SCIP database?
Establish a centralized electronic database or document management system for the SDS library.
Categorize SDSs by product or substance to facilitate easy retrieval.
Implement version control to track updates and revisions of SDSs.
Regularly review and validate the accuracy of SDSs to ensure up-to-date information.
Ensure proper indexing and search functionalities for quick and efficient access to SDSs.
Maintain a backup system to ensure data security and prevent loss of important SDSs.
Have clear procedures in place for retrieving and updating SDSs.
Conduct regular audits of the SDS library to ensure compliance with regulations.
Provide training to employees on how to access and effectively utilize the SDS library.
What information does an SDS document contain?

Identification (Product name, manufacturer, supplier contact information, and recommended uses)

Composition/information on ingredients

Hazard identification

Handling and storage

Facilitating chemical testing and analysis in collaboration with APA's trusted third-party partners.

Exposure controls/personal protection

Disposal considerations
Other information (additional relevant information, such as recommended storage periods and handling precautions)
Challenges with SDS Compliance
How to choose a GHS Hazard Class among the 29 classes available?
How to choose the correct GHS Hazard Pictogram without any legal consequences?
How to classify the process under GHS?
What is the GHS Cut-off Value and Concentration Limit?
How to select appropriate classes for hazardous goods and packing groups?
Understanding the correlation between Section 2 and Section 14
Ensuring compliance across the supply chain
Why Horiaki?

Expert SDS compliance solutions tailored to your business needs
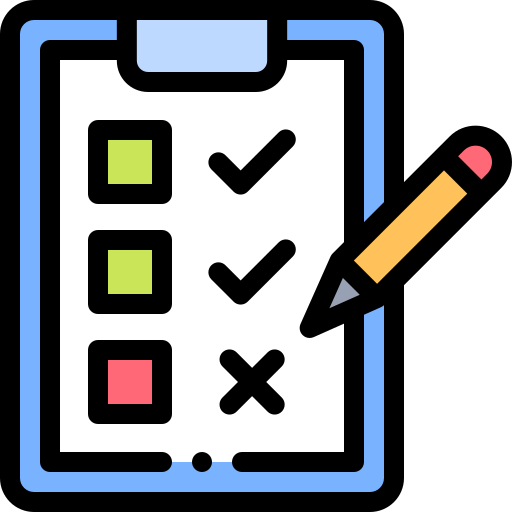
Thorough assessments and audits to identify compliance gaps

Customized compliance strategies to meet regulatory requirements

Comprehensive guidance and support throughout the compliance process

Streamlined compliance journey for enhanced efficiency and productivity

Ensuring the safety and success of your business through compliance expertise.
To ensure compliance with SDS regulations, it is crucial to conduct a thorough assessment of your products and their associated hazards, and then prepare SDSs that accurately reflect the required information.
The specific requirements for SDS preparation and content may vary depending on the jurisdiction, but typically include sections for product identification, hazard identification, composition, first aid measures, handling and storage, exposure controls, and other relevant information.
The process of SDS authoring and updating involves gathering information on the product’s composition, hazards, and safe handling practices, and then organizing and formatting this information in accordance with regulatory guidelines. Regular reviews and updates are necessary to reflect any changes in product formulation or regulations.
SDS translations should be performed by qualified professionals to ensure accurate and compliant translations in the desired languages. Multilingual requirements should be considered based on the regions where the products will be marketed and used.
Proper classification and labeling of products based on SDS information involve understanding the hazards associated with the substances or mixtures, assigning appropriate hazard classes, and applying corresponding hazard symbols, signal words, and precautionary statements on product labels.
Key steps in SDS management and documentation for regulatory audits include maintaining an up-to-date library of SDSs for all products, ensuring accessibility to employees and customers, implementing effective record-keeping systems, and conducting regular audits to verify compliance with regulations and update SDSs as needed.